Какие проекты позволят за три года достичь 50% доли выпуска автомобилей методом CKD
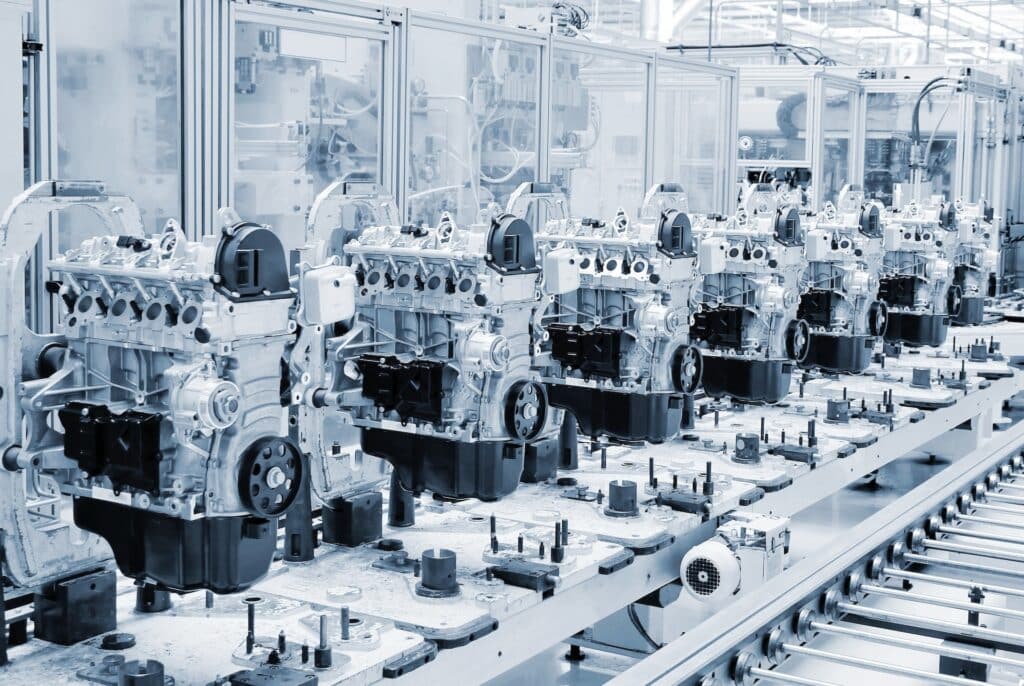
Требования правительства по наращиванию технологической сложности и доли локально производимых компонентов и операций поддерживают и сами участники рынка. Они уверены: на то, чтобы пятикратно повысить долю авто, выпускаемых мелкоузловой сборкой, им потребуется всего лишь три года.
Нынешняя промышленная политика по развитию автопрома начала формироваться около 15 лет назад. После продолжительной эволюции промполитики в этой сфере и того, как выпуск автомобилей перешагнул символическую отметку в 100 тыс., в стране приступили к реализации проектов по локализации автокомпонентов.
Тем самым Казахстан пытается перейти от первого этапа локализации в автомобильной промышленности, который еще не завершен (мелкоузловой сборкой выпускается только 10% от всего объема), ко второму этапу, когда на территории страны для обслуживания потребностей имеющихся производств запускаются площадки по выпуску автокомпонентов. Вторичная локализация как раз позволяет встроиться в цепочку поставок и увеличить добавленную стоимость, созданную внутри страны.
На первой скорости
Платформа действующей промышленной политики по развитию автопрома начала выстраиваться с 2010 года, когда стартовала первая индустриальная пятилетка и Казахстан вошел в Таможенный союз с РФ и Беларусью (ныне ЕАЭС). Тогда же были повышены таможенные пошлины на автомобили (до заградительного уровня). Высокий фактический уровень защиты должен был создать комфортные условия для местных производителей, с которыми правительство РК подписало первые соглашения о промсборке транспортных средств.
Казахстанские автозаводы получили право импортировать компоненты для новых авто и машинокомплекты для крупноузловой сборки (semi- knocked-down, SKD) по нулевой ставке в обмен на обязательство наладить операции по сварке и окраске кузова, монтажу оборудования салона, силового агрегата, рулевого механизма, электрооборудования – то есть тех операций, которые определяются в автопроме как метод мелкоузловой сборки (completely knocked-down, CKD).
Слабым местом первого варианта промсборки оказалось отсутствие критериев, по которым измерялось углубление локализации. В ГПФИИР был заложен целевой индикатор, согласно которому в 2014 году уровень локализации должен был достичь 30%.
Ставка делалась на анонсированное компанией «Азия Авто Казахстан» (компания, входившая вместе с заводом «Азия Авто» и дилерской сетью «Бипэк Авто» в группу «Бипэк») сборочное производство годовой мощностью 120 тыс. автомобилей. Рядом с заводом должен был расположиться технопарк по производству деталей и комплектующих.
Но запуск этих двух проектов, которые в те времена было принято называть автомобильным кластером, откладывался несколько раз. Весной 2020 года правительство РК разорвало соглашение о промсборке со строящимся заводом и действующим предприятием «Азия Авто», которое должно было поставить сварку и окраску до конца 2019-го. В августе 2020-го преференции были отозваны, обе компании обязали вернуть в бюджет недополученные 174 млрд тенге. В конце июля 2021 года контролирующий акционер компаний Анатолий Балушкин был объявлен в розыск.
Больше индикаторов
Переходным в непростых отношениях государства и автопрома следует считать 2020 год. Завершилась вторая пятилетка; в казахстанском автопроме уровень локализации, по оценке отраслевых экспертов, приблизился к 35%, хотя еще в середине 2018-го Высший евразийский экономический совет закрыл доступ на рынок ЕАЭС для автомобилей с локализацией менее 50%. Неудачный кейс с «Азия Авто Казахстан» сбавил оптимизм у чиновников, ответственных за развитие обрабатывающей отрасли, и убедил их быть к строже к автопроизводителям.
В 2020 году завершились старые соглашения о промсборке. В новых условия были ужесточены. Чтобы стимулировать производителей сокращать объемы производства SKD в пользу CKD, ввели балльную систему оценки локализации, которая годом ранее была опробована в России.
Баллы начисляют за локализацию сборочных операций, использование изделий и компонентов, произведенных в Казахстане или в странах ЕАЭС. Из сборочных операций дороже всего оценивается локализация сварки и окраски кузова дополнительной модели транспортного средства (1 тыс. баллов), из изделий и компонентов – локальные двигатели, КПП, аккумуляторная батарея, колесные диски, шины и бамперы (500 баллов).
К моменту заключения соглашения у автопроизводителя локализация должна быть на уровне 3 тыс. баллов. После заключения соглашения бизнес принимает обязательство увеличивать каждые пять лет пороговое значение на 2 тыс. баллов, иначе договор будет расторгнут. Автопроизводитель обязан возместить все льготы, которые он получил в рамках этого соглашения о промсборке.
В мае 2022-го правительство опять ужесточило требования в соглашении о промсборке, повысив порог вхождения новых игроков. В предыдущем списке начальных требований указывались сварка и окраска кузова не менее двух моделей. В новом варианте – сварка и окраска не менее одной модели по каждой производимой марке.
Раунд ужесточений продолжился в текущем году. Этому предшествовала президентская критика, направленная на обрабатывающую отрасль в целом. Как отметил Касым-Жомарт Токаев, уровень локализации следует неуклонно повышать, идти от простого к сложному. «Такие примеры уже имеются, но есть также факты подмены понятий за счет ложной локализации», – добавил глава государства на правительственном совещании в апреле 2023-го.
После этого, в марте 2024-го, вышла новая редакция соглашения о промсборке. Действующая балльная система была дополнена еще одним количественным показателем – долей мелкоузловой сборки. Автопром должен нарастить ее с 20% в 2024 году до 50% по результатам 2027-го.
Планка в 50%
По состоянию на апрель 2024 года в РК действует восемь соглашений о промсборке транспортных средств, из которых две заключены с производителями легковых автомобилей – Hyundai Trans Kazakhstan и «СарыаркаАвтоПром». Министерство промышленности и строительства РК также заключило такие контракты с производителями спецтехники и автобусов: Daewoo bus Kazakhstan, Hyundai Trans Аuto, QazTehna и «СемАЗ», «КамАЗ-Инжиниринг» и «Уральскагрореммаш».
Сейчас в Казахстане выпускают легковые автомобили две компании – костанайский «СарыАркаАвтопром» (входит в группу Allur) и алматинский Hyundai Trans Kazakhstan («дочка» компании «Астана Моторс»). Эти автомобильные компании в следующем году намерены запустить два проекта.
Один из них – это завод по производству автомобилей Kia годовой мощностью в 70 тыс. единиц. Еще до введения нового целевого ориентира Allur пообещал, что 50 тыс. автомобилей будут собираться методом CKD. В конце 2023 года компания распространила информацию о том, что пилотный запуск завода состоится в первом квартале 2025-го, во втором – откроется полный цикл производства.
Мультибрендовый завод полного цикла, где, как обещает «Астана Моторс», методом мелкоузловой сборки будет выпускать марки Chery, Haval и Changan. Общая мощность этого предприятия – 90 тыс. автомобилей. Завершение строительства запланировано на февраль 2025 года. Цель «Астана Моторс» – перейти на 100% мелкоузловое производство со сваркой и окраской кузова в 2027 году.
В марте 2024-го компания Orbis Kazakhstan, в составе которой есть автомобильное подразделение Orbis Auto (официальный дилер нескольких брендов), распространила информацию о том, что во II квартале текущего года начнет строительство автомобильного завода полного цикла Orbis Manufacturing в Индустриальной зоне Алматы. Его годовая мощность составит 80 тыс. автомобилей. Между Orbis Kazakhstan и китайским Yibin Kaiyi Automobile подписан меморандум. По предварительным договоренностям, китайский партнер предоставит Orbis Kazakhstan всю необходимую техническую документацию на продукцию, а также направит технических специалистов на место для оказания поддержки и обеспечения технологического контроля. Пока что нет информации о том, какая доля автомобилей будет производиться мелкоузловой сборкой.
В минувшем году казахстанские производители выпустили 134 тыс. легковых авто, методом CKD было собрано лишь чуть менее 10%. Есть основания полагать, что в прошлом году автопром вышел на полную загрузку мощностей.
Если допустить, что количество автомобилей, выпущенных методом SKD, сохранится в этом объеме, то с учетом заявленного выпуска авто методом CKD (50 тыс. + 90 тыс.) доля мелкоузловой сборки достигнет 56% (или порядка 153 тыс. авто). Между тем министр промышленности и строительства РК Канат Шарлапаев прогнозирует выпуск многоузловым методом порядка 200 тыс. автомобилей.
Двигатель промышленного разгорания
Соглашение о промсборке за годы формирования промышленной политики по развитию автопрома стало ее центральным элементом. Кабмин на основании соглашения о промсборке и заключенных инвестиционных контрактов предоставляет предприятиям ряд налоговых и таможенных преференций, включающих освобождение от уплаты НДС при импорте комплектующих и реализации готовой продукции, а также от ввозной таможенной пошлины на машинокомплекты. Еще возвращается уплаченный утилизационный сбор. Компенсации позволяют снизить стоимость транспортного средства для конечного потребителя, делая собранную в Казахстане продукцию дешевле импортированной.
Промышленная политика в 2020 году пополнилась еще одним элементом – соглашением о промсборке компонентов, которое, наряду с соглашением о промсборке транспортных средств, делает систему более сбалансированной. Этому предшествовало то, что на уровне правительства начали чаще вспоминать, что локализацию автомобильного производства делят на два вида – локализацию процесса (окраска, сборка рамы, сварка деталей) и локализацию компонентов (выпуск деталей и комплектующих).
Казахстанский автопром в 2022 году преодолел планку в 100 тыс. выпущенных авто – символическое для отечественного автобизнеса число, после которого, как считают производители, проекты по углублению локализации становятся экономически целесообразными. И местные компании начали презентовать собственные проекты по локализации автокомпонентов либо привлекать партнеров к этому делу.
Группа Allur летом прошлого года объявила о строительстве в Костанае локализационного центра по производству автокомпонентов (в индустриальной зоне города, рядом с новым заводом Kia). Мощность центра составит 70 тыс. комплектующих в год. Там в первую очередь планируют локализовать производство проводов, бамперов, сидений, выхлопных систем, сэндвич-панелей. Это крупногабаритные детали, из-за чего их на профессиональном сленге называют «воздухом», локализация которых позволит сэкономить на логистике.
В Индустриальной зоне Алматы, рядом со строящимся мультибрендовым заводом, планируется запустить три проекта по локализации компонентов. По словам СЕО «Астана Моторс» Бекнура Несипбаева, есть договоренности с инвесторами из Южной Кореи. Одна компания начнет в августе выпускать сиденья, будет функционировать линия по отливу подушек; ожидается, что как только производство перейдет рубеж в 50 тыс. авто, появятся швейные цехи для шитья чехлов из отечественных материалов. Второй проект – выпуск мультимедийных систем. «В среднем производство сидений в Казахстане даст снижение цены около $82 на одно авто, мультимедийные системы снижают цену машины на $100», – прогнозирует Несипбаев. Также ведутся переговоры с третьим возможным инвестором по созданию резиновых технических изделий. Компания одновременно с этим ведет переговоры с местным МСБ по поводу производства мелких деталей.
Пока что действуют шесть промсборок компонентов для транспортного средства (на апрель 2024-го): Stahlbau (прочие кузова для моторных транспортных средств), Kama tyres (шины), «Кайнар-АКБ» (электрические аккумуляторы), KamLitKZ (главная передача ведущего моста грузового транспортного средства, блок цилиндров и головка блока цилиндров двигателя грузового транспортного средства, картер ведущего моста – балка), «Уральскагрореммаш» (кузова), TehnoPark (прочие части и принадлежности кузовов для моторных транспортных средств).
Готовы в РК замахнуться и на более сложную задачу. По информации Минпрома, на комбинате Qarmet (родственная Allur компания) планируется наладить производство автомобильной стали для последующей организации технологических операций по штамповке компонентов кузова автомобиля.